Unlike most ICF systems, the TF form segments are oriented vertically, which makes them especially well suited for tall walls. The system consists of four main components:
• Panels made of 2½ -in.-thick, highdensity, rigid polystyrene.
• Corner sets made of rigid, recycled
PVC.
• Stud rails available in either rigid, recycled PVC (standard) or 26-gauge galvanized steel.
• C-channels made of 27-gauge galvanized and painted steel.
• Panels made of 2½ -in.-thick, highdensity, rigid polystyrene.
• Corner sets made of rigid, recycled
PVC.
• Stud rails available in either rigid, recycled PVC (standard) or 26-gauge galvanized steel.
• C-channels made of 27-gauge galvanized and painted steel.
The vertical orientation is designed to prevent the wall forms from floating and settling, and to provide a dimensionally accurate wall. With no need to glue, tape, or tie components together, assembly is simple and efficient. The basic components form the walls, provide insulation, create a vapor barrier, and serve as convenient and predictable attachment points.
The TF System requires no special concrete mix design beyond a recommendation to use a 4- to 6-in, slump and aggregates of 3/4 in. or smaller, to make sure concrete flows freely around the stud rails. The concrete should he placed in approximately 4 foot lifts.
Contractors typically consolidate concrete in the system using the same techniques as with any other form, though Spude says that TF’s foam panels are sturdier and less prone to blowouts than some lighter-duty residential ICFs.
The company is currently managing Construction of 120, 000-sq. -ft. residence in Highlandville, Mo., that Spude describes as a “modern-day castle” with some walls that are 16 ft tall. To facilitate the consolidation of the lower 8 ft of wall (the first two lifts), the contractor is using a Rehar Shaker, manufactured by Oztec Industries, Port Washington, N.Y. These tall walls contain No. 5 vertical reinforcing bars, 16 in. on center.
To operate, one person attaches the shaker to the top of the bar, centers the bar in the wall cavity, and turns on the shaker while the concrete is placed. The vibration of the rebar serves to eliminate voids and consolidate the concrete, much as the steel or rubber head does when using a conventional pencil vibrator.
“This is our first job using the rebar shaker,” Spude says, “and it’s saving a lot of man-hours and shoulder strain. The crews don’t have to move the vibrator up and down during the pour, so it’s quite a bit easier for them. After the first two lifts, we’re using standard insertion-head vibrators to consolidate the tops of the walls. This method seems well suited for tall concrete wall construction, whether it’s with ICFs or other types of forms.”
The TF System requires no special concrete mix design beyond a recommendation to use a 4- to 6-in, slump and aggregates of 3/4 in. or smaller, to make sure concrete flows freely around the stud rails. The concrete should he placed in approximately 4 foot lifts.
Contractors typically consolidate concrete in the system using the same techniques as with any other form, though Spude says that TF’s foam panels are sturdier and less prone to blowouts than some lighter-duty residential ICFs.
The company is currently managing Construction of 120, 000-sq. -ft. residence in Highlandville, Mo., that Spude describes as a “modern-day castle” with some walls that are 16 ft tall. To facilitate the consolidation of the lower 8 ft of wall (the first two lifts), the contractor is using a Rehar Shaker, manufactured by Oztec Industries, Port Washington, N.Y. These tall walls contain No. 5 vertical reinforcing bars, 16 in. on center.
To operate, one person attaches the shaker to the top of the bar, centers the bar in the wall cavity, and turns on the shaker while the concrete is placed. The vibration of the rebar serves to eliminate voids and consolidate the concrete, much as the steel or rubber head does when using a conventional pencil vibrator.
“This is our first job using the rebar shaker,” Spude says, “and it’s saving a lot of man-hours and shoulder strain. The crews don’t have to move the vibrator up and down during the pour, so it’s quite a bit easier for them. After the first two lifts, we’re using standard insertion-head vibrators to consolidate the tops of the walls. This method seems well suited for tall concrete wall construction, whether it’s with ICFs or other types of forms.”
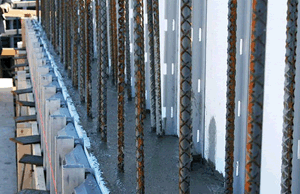
With forms braced, crews direct pumped concrete betweem foam panels.
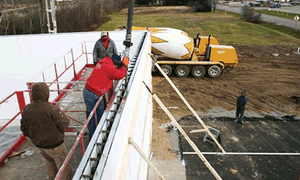
To operate the rebar shaker, one person attaches it on top of the bar, centers the bar in the wall cavity. And turns on the shaker while the concrete is placed.
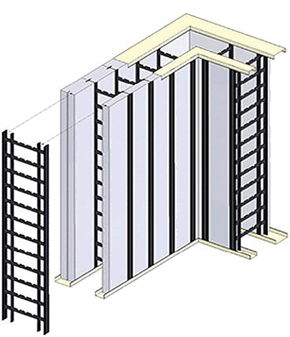
The TF System Inc.’s vertical ICF design consists of polystyrene foam panels, steel or recycled PVC stud rails, corner sets, and C-channels.
No hay comentarios:
Publicar un comentario