And when Simpson Gumpertz & Heger Inc. (SGH) was offered the opportunity to structure one of his crown jewels, it was truly a humbling experience for the entire design team.
St. Nicholas Constantine and Helen is a Greek Orthodox Church complex in Roseland, N.J. The project consists of a main church building, a school building, a central rotunda and a gymnasium/social hall. Spread over 39,000 sq. ft, the complex is a visual delight with the centerpiece being the main church building with its characteristic Byzantine design.
Design for the building started in early 2006. From the very beginning, steel was the primary material of choice for all except the main church building. Given the many curved and faceted roofs intersecting with each other, the design team initially considered concrete for the main church building. After considerable research and discussions, the decision was made to use curved structural steel combined with curved metal studs. One reason for this was to eliminate mixing of trades. Because the remaining portion of the facility was going to be framed in steel, it was prudent to use one material which would streamline the entire construction process. Additionally constructing a concrete dome would have required special expertise and likely would have driven up the overall construction cost. The fact that a concrete dome would weigh substantially more also would have increased foundation costs. One concern about using steel was the considerable amount of field welding required, but that single factor was not enough to tilt the balance in favor of concrete. In retrospect, this decision has proven to be a good one.
The progression from design drawings to shop drawings to fabrication and erection was completed smoothly with minimal glitches. West Coast mentality for complete connection details on the contract documents was, at least to some degree, helpful in attaining this achievement. The decision to use steel also reduced the number of trades involved in the superstructure and improved the construction schedule. At the same time, a slump in the construction industry in mid-2008 enabled the church to get a much more competitive bid for the complex church building with its ornate design and curved steel framing.
The church complex can be separated into three segments. The first is the education/school building complex, a single-story 60-ft by 150-ft building with one level of basement. The main floor at grade consists of 4½ in. normal weight concrete over B decking and open web steel joist framing. The lateral system for the above-grade structure consists of cold-formed bearing wall with plywood sheathing. Although constructed as a single-story structure, there was a clear directive from the owner to design it considering a future expansion of one level. Accordingly, SGH designed a pseudo floor below the roof with standard floor loading and placed the steel trusses above this floor. This was done so that in the future, if required, the owner can simply remove the roof trusses, build one level of framing and reuse the roof trusses.
Although the addition of this extra floor increased the initial construction cost, there were tremendous gains from this decision. First, this pseudo floor gave the owner the flexibility of adding an extra level without having to worry about possible additional costs of retrofitting the gravity system had it been designed as a single-story structure. Second, the classrooms can continue to function as the new floor is being added, whereas they would certainly have to be relocated, albeit temporarily, for the retrofit option. Although a detailed cost benefit analysis was not conducted, common sense evaluation tells us this was a prudent investment that the owner chose to make up front in order to reap the benefits later.
The main church is roughly 100 ft square in plan with a vertical height of 35 ft to the dome base. The dome, approximately 50 ft in diameter, rises another 15 ft from the springing level culminating in the traditional cross at the top. The main lateral system for the dome is provided by eight 24-in. diameter pipes with a moment-connected continuous HSS20r12r5⁄8 member at the eave level (29 ft above the floor). Eight inclined W14 cantilevers attach to the pipe columns at that level and rise up to receive the base for the dome. The dome itself is made up of 20 curved HSS10r4r3⁄8 ribs connected by a ½-in.-thick continuous compression ring at the top. In addition, there is sub-framing consisting of curved or piece wise linear cold-formed stud framing that makes up the surface of the dome.
The curved ribs supplied by the fabricator were welded to the compression and tension ring in place and provided perhaps the single most challenging aspect of the whole dome construction. It took the con-tractor roughly three weeks to finish welding the ribs. Unfortunately the timing also coincided with the summer rains, which resulted in considerable interruptions during the construction. Apart from the domed portion, the church building also has a two-story choir loft that is a steel braced frame structure with composite steel framing.
The main church building gradually meanders into the gymnasium area via a rotunda with a domed roof framed in a similar way as the main church dome. The gymnasium building is a large open area, 100 ft by 100 ft, with the roof framing consisting of non-composite roof decking over open web steel joists. The lateral strength is provided by steel braced frames with the roof decking serving as the diaphragm. In addition, there are several low-level structures around the perimeter supported by cold-formed stud bearing walls with ply-wood sheathing.
The foundation system for the three buildings is a combination of isolated footings and continuous strip footings underneath the bearing walls. Braced frames are supported on combined footings. Perimeter footings are founded 4 ft. below the adjacent grade due to frost concerns.
The International Building Code 2000 New
Jersey Edition was used for the design of the buildings. A ground snow load of 25 psf was considered for all roof design. In addition, several cases of unbalanced and drift snow loading were considered due to the complicated roof levels and shapes. Generally wind governed the lateral design for most cases (Basic Wind Speed = 100 mph, Exposure B) although SGH performed a response spectrum analysis on the main church building in the spirit of a true West Coast design firm.
Another paradigm shift for SGH-San Francisco was setting up the design documents to suit East Coast fabricators. This applied especially to the connections, both gravity and lateral. Whereas a single welded shear plate with bolted web is the most common west coast gravity connection, a conversation with our colleagues in our Boston office revealed that welded double angles with bolted web is what N.J. fabricators are used to seeing. Additionally, where a West Coast drawing will typically lay out all the connection details for the lateral system, significant freedom is given to the East Coast detailer for designing such connections with only the required connection force mentioned in the drawings. In the end, the detailing of the gravity and lateral connections approached West Coast thoroughness and connection forces were specified for the detailers. The net result was that the detailers clearly understood the design intent, but still had flexibility to adjust the details in accordance with East Coast shop practice. Although such differences never created major impact, there were several spirited “Oh you California guys” type of conversations with the detailer during the shop drawing phase.
As the design phase transitioned into the shop drawing phase, we quickly realized the enormity of the problem of shipping three sets of shop drawings back and forth across the country.
Not only was cost a concern, but also the time lag involved in a reasonable mode of delivery. Technology provided a solution and greatly simplified the process. Drawings mostly were transferred over the Internet in PDF format, checked and marked in the editor and emailed back to the fabricator. Not only did this save time, we also managed to save a few trees in the process.
At the time of publication of this article, steel has been completely erected with the interior improvements progressing in full swing. With the passing of every milestone, the view looks more similar to the artist’s rendering bringing smiles to the members of the design team. This project demonstrates once again that structural steel can accommodate unusual and complex shaped structures and result in competitive costs and meet schedules.
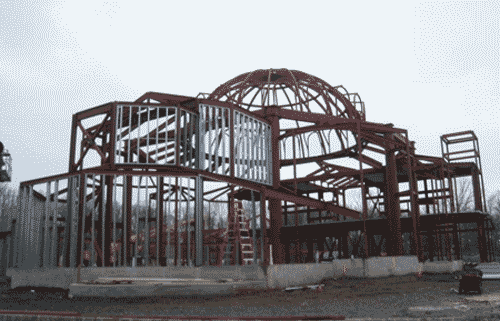
^Structural steel being erected for the church building
No hay comentarios:
Publicar un comentario